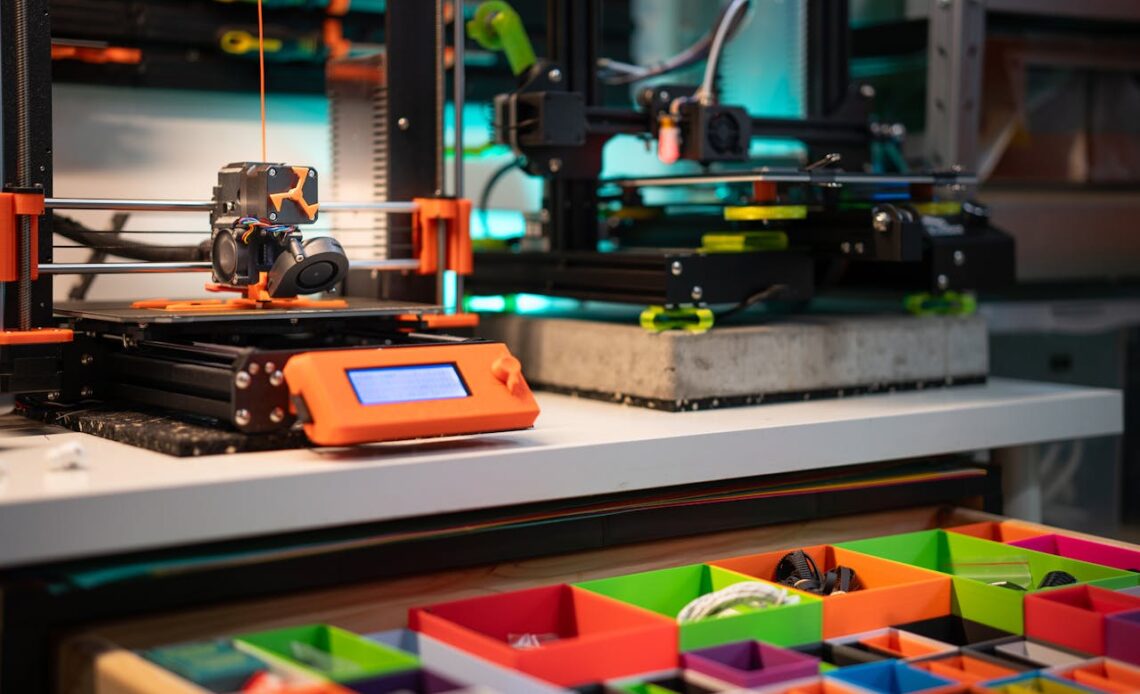
In the last decade, 3D printing in UAE has taken off in popularity due to a combination of factors including open-source printers, affordable desktop machines and accessible print materials. Unlike traditional manufacturing technologies, it doesn’t require a block of material or a mold to produce physical objects; instead, it stacks and fuses layers of powder.
Additive Manufacturing
Additive manufacturing is a process of creating physical objects directly from a three-dimensional digital model, using layers of print material to build up the object. There are many different ways to do this, with some printers using plastics, others using metals and others still printing in concrete or other materials. The layer-by-layer construction makes it possible to create complex geometries that would be impossible or very expensive to produce with traditional methods, allowing for faster prototyping and reducing production time and costs.
For manufacturers, it means they don’t have to wait for a supplier to make the tooling needed for conventional manufacturing, which can slow down projects. And it allows them to keep projects in-house, which can protect intellectual property and other proprietary innovations.
3D printing also makes it possible to make custom parts for specific people, which can be useful in fields such as medicine. For instance, an orthopedic specialist could 3D print a custom-fitted insole for a patient. And nonprofits that address issues such as homelessness can use massive 3D printers to construct whole neighborhoods, like the New Story project in Mexico, whose 33-foot long printer is capable of churning out a 500-square-foot home in just 24 hours. As the technology develops, it may even be able to print houses with walls, windows and furniture.
CAD Design
3D printing turns a digital CAD (Computer-Aided Design) model into a physical, three-dimensional solid object. It is called additive manufacturing because it layers the material rather than cutting the solid into thin sections like traditional production methods do.
Once the 3D printing software converts the CAD model into machine instructions, the printer essentially operates like an inkjet printer, adding a layer of wax or plastic-like polymer to the print bed one at a time. The nozzle waits for each layer to dry before dispensing the next one. This process is repeated hundreds or thousands of times to create the final 3D object.
A few of the major types of 3D printing materials include polylactic acid (PLA), acrylonitrile butadiene styrene (ABS), carbon fiber and metals. The choice of a particular material depends on the desired properties of the finished product. For example, PLA is derived from organic, renewable resources and easy to work with, while ABS has better temperature resistance but can be tougher to print with than other materials.
Originally, the concept for 3D printing was to speed up industrial product development by eliminating the need for costly prototyping. Inventor Charles Hull is credited with creating the first 3D printer, which used the stereolithography process, in 1984. His company, 3D Systems, went on to develop other printing techniques that included sintering and melting.
Layered Printing
Once the virtual design is made, it is broken down into flat layers that are easy for the printer to read. Each layer consists of a perimeter and infill that will create the shape of the finished product.
Each layer is deposited on top of one another in sequence until the object has been completed. The most common 3D printers use powder-like materials such as plastic, but it’s possible to print with metals like carbon fiber and even biomaterials. It is a very flexible process that allows a wide variety of applications.
Some of the most popular printing methods include selective laser sintering, direct energy deposition, powder bed fusion and stereolithography. Selective laser sintering uses heat to bind together powder grains of different plastics or metals. Powder bed fusion and direct energy deposition use lasers, electric arcs or electron beams to melt or fuse the material into a solid form. Finally, stereolithography uses light to curing special photopolymers in a liquid resin to create parts.
As a powerful and innovative technology, 3D printing is changing the way that we make things. It can reduce the time it takes for a new product to be developed, from conception to production and distribution. It can also help companies produce replacement parts quickly and inexpensively, making repair and maintenance a breeze.
Material Jetting
Material jetting, also known as polyjet printing and binder jetting, is one of the fastest 3D printer technologies available. This print process sprays micro-droplets of liquid photopolymer resin onto the build platform and cures them with UV light, similar to traditional inkjet printing. It then builds layer by layer until the object is complete. MJ can use both rigid and rubber-like materials and can offer high levels of detail, surface finish and color accuracy, making it perfect for creating realistic prototypes.
With a wide variety of colors and materials to choose from, designers can create a model that closely resembles the final product, offering an exceptional level of realism. It is especially good for producing prototypes that need to comply with specific requirements (e.g. temperature resistance, biocompatibility, stiff or flexible).
The advantage of MJ over other 3D printing methods is that unlike point-wise deposition technologies that draw parts with a single laser or nozzle, material jetting deposits print materials in a continuous line. As a result, MJ can achieve much higher print speeds and can produce a part in multiple materials or colours simultaneously.
The rapid growth of 3D printing offers businesses a unique opportunity to differentiate themselves in the market. However, keeping up with this constantly evolving technology can be challenging. That’s why it’s important to entrust your print projects to professionals who can help you stay ahead of the competition and deliver the best results.